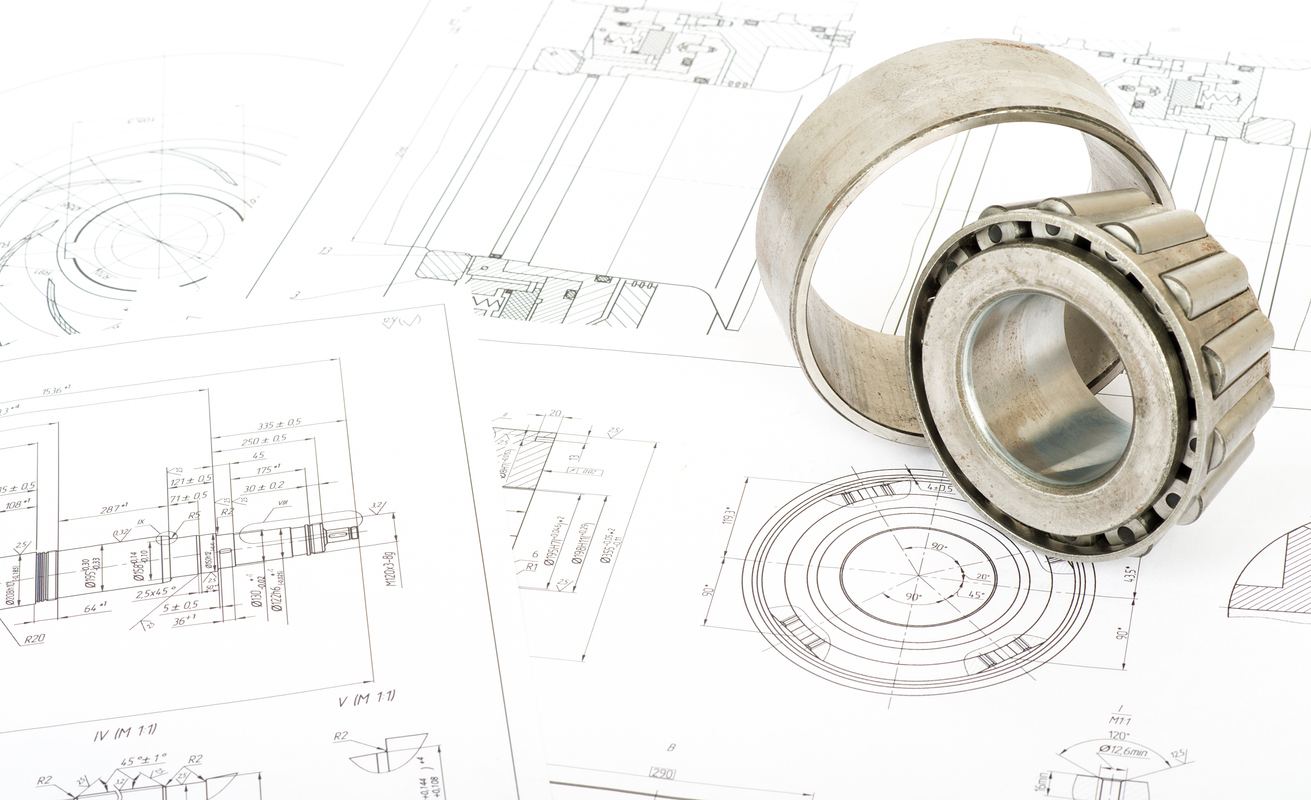
Engineering Services
Utilizing cutting-edge technology, our engineering team designs and refines solutions tailored to your needs. We can turn any challenge into an opportunity.
Learn MoreAlco is a precision machine shop built on over 50 years of success. With seven locations, renowned customer service, and robust capabilities, we’re ready to take on your next project.
As a trusted precision machine shop with over 475,000 square feet of manufacturing space, we’re the partner of choice for companies like yours. From design and manufacturing to secondary processes, we’ve got you covered.
Utilizing cutting-edge technology, our engineering team designs and refines solutions tailored to your needs. We can turn any challenge into an opportunity.
Learn MoreWe have 398 multi-spindle screw machines, 109 CNC machines, 27 rotary transfer hydromat machines, 41 single-spindle machines, and 7 multi-spindle CNC machines.
Our advanced systems deliver high-volume, precision machining with unmatched efficiency, ensuring consistent quality for even the most complex components.
Learn MoreWith state-of-the-art milling and turning capabilities, we craft precision parts for industries that demand accuracy. Our cutting-edge equipment allows us to meet your every need.
Learn MoreOur multi-spindle screw machines are designed for high-speed production of complex parts. This allows us to produce large volumes of high-quality components while minimizing cycle times.
Learn MoreWe provide a range of secondary services to ensure your parts meet your exact specifications. With our services, you can streamline production and superior quality.
Learn MoreMany industries require intricate, high-precision parts. Our Swiss machining expertise allows us to create small-diameter, complex components with ease.
Learn MoreAlco is a precision machine shop built on over 50 years of success. With robust capabilities, we’re ready to take on your next project. Learn more.
Learn MoreFor over 50 years, we’ve been helping businesses get the right machined parts for their needs. Our dedication to quality has made us one of the largest domestic suppliers of precision machined components and fittings in steel, stainless steel, brass, and aluminum.
Our strength is in our size, which allows us to provide a range of capabilities at the best price possible. Our company now spans seven facilities across the Great Lakes area from Michigan to New York.
Looking for a quick solution for your business? Stock machined parts don’t require excessive design or testing time, making them an ideal solution for companies in all industries. View our catalog for time-tested parts that can help you get to market faster.